CNC BRIAN
CNC Machining
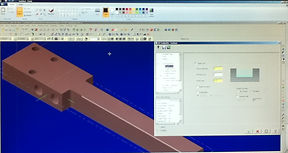
SAMPLE PROGRAMS
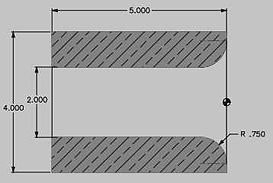
N1 T01 G20
N2 G00 X3.5 Z0.5
N3 G01 G96 S120 Z0 F.5
N4 G02 X2 Z-.75 R0.75 F0.15
N5 G01 Z-5 F0.2
N6 G01 X1.85N7 G00 Z20
N8 M30

N10 T303
N20 G97 S4000
N30 G20 M03
N40 G00 X0 Z0.5
N50 G01 Z0 F0.003
N60 X0.5 R0.1
N70 Z-0.65
N80 X0.7 C0.06
N90 Z-1.15
N100 X0.75
N110 X0.875 Z-1.8
N120 X0.925
N130 Z-2.05
N140 X1
N150 Z-3
N160 G28 U0. W0.
N170 M30
FANUC G71 AND G70 CANNED CYCLE

N40 G97 S2500 M13
N45 T505
N50 G50 S4000
N50 G96 1250
N90 G01 Z-75
N50 G00 X106 Z5 M3 S800
N60 G71 U10 R10
N70 G71 P80 Q90 U3 W0 F0.25
N80 G00 X60
N90 G01 Z-75 F0.15
N100 G00 X200 Z100
N110 G92 S1200
N120 T3 G96 S150 M03
N130 G00 X106 Z5
N140 G70 P80 Q90
N150 G00 X200 Z100
N160 M30
First-cut
1 – Tool will move in x-axis U (depth of cut) deep with programmed feed from starting-point.
2 – Tool will travel with feed in z-axis (destination point in z-axis is given in P Q blocks )
3 – Tool rapidly retracts R amount in both x-axis and z-axis (at 45 degrees).
4 – Tool rapidly travel in z-axis to start-point
Later-cuts
5 – Tool rapidly moves to last cut depth.
6 – Tool moves with feed in x-axis U deep (first-block U depth of cut).
7 – Tool with feed moves in z-axis (destination point given in P Q blocks).
8 – Tool rapidly retracts in x-axis and z-axis R amount (45 degrees).
9 – Tool rapidly moves to start-point only in z-axis.
This whole sequence of operation keep on going, until the destination point in x-axis is met.
If finishing allowance is given tool will not make the exact diameter and length given in P Q blocks but will leave that much allowance, This finishing allowance can be later machined by calling G70 finishing cycle.
FANUC G76 THREADING CYCLE

This tells how cnc machinists can change following values with G76 threading cycle parameters, Depth of cut for First pass, Depth of cut for normal passes, Depth of cut for Last pass, Control number of Spring passes.
N20 G97 S500 M13
N25 T101
N30 G00 X30 Z5
N40 G76 P021060 QI00 R100
N50 G76 X18.2 Z-20 P900 Q200 FI.5
N60 G00 X50 Z-20
N70 G76 P021060 Ql00 R100
N80 G76 X38.2 Z-52 P900 Q200 FI .5
N90 G00 X200 Z200
N100 M30
Depth of First Pass
With Q parameter in second-block of G76 threading cycle you can change the threading depth of First-pass of threading operation.
In the above code Q200 value is given so while threading our tool will take 0.2(mm or inch) deep cut for the first pass.
Depth of Each Pass
For remaining passes depth of cut G76 use First-block Q parameter which is given above as Q100 (0.1 mm or inch).
Depth of Last Pass or Finish Cut
Last of Finish cut is also programmed with G76 as in above code First-block R parameter is given R0.05 (0.05 mm or inch)
Number of Spring Passes
Once the threading cycle has completed the Finish-cut (R parameter in first-block) you can program tool to take extra passes (spring pass) on the same depth for multiple times (to smooth or finish thread surface).
Spring passes can be controlled through P parameter in First-block of G76 threading cycle
P : P actually control three different values which control the thread behavior,
-
01 : Number of spring passes or spring cuts.
-
00 : Thread run out at 45 degree
For spring pass control only first pair value is used of P parameter, as above 01 is given, the tool will take one extra pass, you can change this value according to your requirements.
FANUC G75 GROOVING CYCLE

N10 T1212
N30 G97 S400 M13
N40 G00 X110 Z0
N50 G01 Z-22 F0.5
N60 G75 R1
N70 G75 X90 Z-60 P2000 Q3000 R0 F0.1
N80 G00 X120 Z100
N90 M30
The grooving tool is 4mm wide, so I started from z-22.
Every time the grooving tool will take 2mm (P2000) cut in x-axis, and it will retract 1mm (Pecking, First R1)
After a groove in x-axis is complete it will start the next groove by moving the grooving tool by 3mm (Q3000) in z-axis, and it will repeat it.
CNC Arc Programming G02 G03
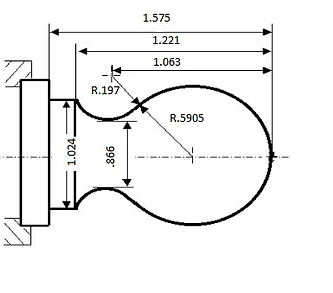
O0001
(FINISH PASS)
N001 T303 (Tool Change)
N002 G0 X1.575 Z.197; (Rapid position)
N003 G97 S2000; (Start spindle)
N004 G01 X0 Z0 F.004ï¼› (Approach workpiece)
N005 G03 U.945 W-.945 R.5906; (Cut R.5906 arc)
N006 G02 X1.024 Z-1.22 R.197; (Cut R.197 arc)
N007 G01 Z-1.575; (Cutф1.024)
N008 X1.575 Z.197ï¼› (Return to starting point)
N009 G28 U0. W0. (Return to home position)
N009 M30; (End of program)

I ran this program on a Hardinge T-42 with a Fanuc 18T controller to prove it works!
Heres the finished product!